Projects
Barge Unloading & Rail Car Loading
Location: Evansville, IN
Materials: Iron Carbide
Material Handling Rate: 400 TPH minimum
- System for barge unloading & rail car loadout
- Conveyors reated at 400 tons per hour minimum
- Truss and support designed for 100 MPH winds
- Conveyors equipped with pulse-jet dust collectors
- Ceramic lined discharge chutes and transitions
- Dual idler belt scales provided
- Operators control room and platform
- Electric powered telescoping loadout spout
Wilson Manufacturing & Design, Inc. was uniquely involved in the design and construction of this storage and distribution terminal for a client in Evansville, Indiana.
The purpose of this terminal is to unload and store iron carbide from barges to a new storage dome, where it can be transfered to rail cars on demand. The equipment utilized is designed to handle the material at a rate of 400TPH minimum.
A loadout hopper and conveyor were provided to receive the stored material from endloader and transfer the material to rail cars at a rate of 400TPH minimum. The hopper is constructed of heavy gauge mild steel with an abrasion resistant liner, adjustable flow baffles, and an air operated slide gate.
A 180' long 36" belt, box truss type conveyor designed to span existing rail track and road, transfer the material to a 90' long conveyor to feed the dome.
A 200' long 36" belt loadout conveyor and supports were provided to transfer the material from the hopper to rail cars. The design of the loadout equipment is of the same high quality construction as the barge unloading system and utilizes the same top quality brand components and instrumentation.
A walkway with non-skid grating is provided full length of the conveyors, giving access to all service platforms located at the drive areas, gravity take-ups, and dust collectors.
The loadout conveyor is equipped with a dual idler belt scale with an accuracy of +/- 1/2%. The belt scale control panel includes LCD diplay of belt speed, rate of transfer in T.P.H., and running total. The unit is also provided with a master totalizer, NEMA 4 enclosures, and automatic zero.
Due to the abrasive and dusty nature of iron carbide, special considerations were made in the design of the chutes and transitions are enclosed to limit rain and control dust and, all wear surfaces are lined with bolt in ceramic wear plates. The belts are covered with hinged type full covers which open independently for easy serviceability. 2000 ACFM pulse-jet dust collectors are provided at all trasfer points to control dust.
A telescoping loadout spout with dust collector pick-up is utilized to control dust when loading rail cars. The loadout spout has a cone bottom for self-aligning in the rail car hatch, 10' of verticle travel, and electric push button controls. The controls for the conveyor are located in a control room on the operator platform. The control room location provides the operator with good visibility of approaching rail cars and positioning of the loadout spout.
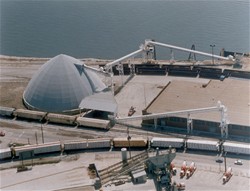